Economical, reliable and easily automated, ultrasonic welding is a popular technique in the plastics welding industry. Ultrasonic welding differs from more traditional forms of welding, where heat is generated through contact with a direct heat source.

Amplitude, Frequency & Wavelength
In ultrasonic welding, longitudinal waves are transmitted at high frequencies to create low-amplitude mechanical vibrations. Electrical energy is converted to reciprocating mechanical energy in the ultrasonic welding equipment. To understand the relationship between amplitude, frequency and wavelength and how this relates to the creation of heat, the main components of the ultrasonic welding equipment must be considered.
The equipment has a power supply, converter, booster and a sonotrode. The power supply changes mains electricity from 50-60 Hz into an electrical supply operating at 20-40 kHz. This energy is supplied to the converter, which changes this electrical energy into mechanical vibrations using discs of piezoelectric material – which are physically altered when an electric current is passed through them.
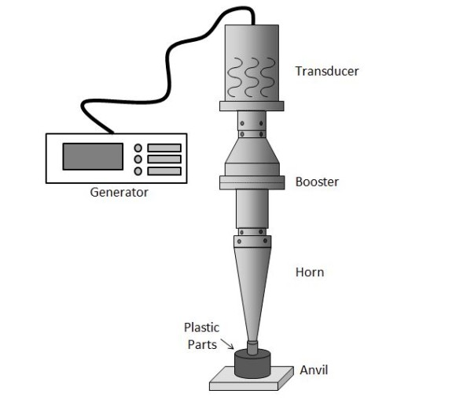
The converter transmits these vibrations to the booster, which is used to increase the amplitude of the sound wave. In turn, the booster transmits amplified sound waves into the sonotrode, which makes contact with the components to be welded.
This energy is concentrated to a specific apex point between two joining materials using the sonotrode, which is held under pressure onto the materials held in the fixture. Heat is then created by two kinds of friction – the external surface friction between the two materials being welded and the internal intermolecular friction within the materials. It is this heat generated by friction that causes the materials, which are held under pressure, to melt and weld together.
Understanding The Heating Rate
The combined effect of the frequency, amplitude and clamping pressure determines the rate of heating. As frequency is usually fixed for a given machine, the heating rate can generally be modified by the clamping force. Typically, the higher the force, the quicker the heating rate, but this is not the only factor that determines heating rate. Amplitude can have a large bearing on cycle time and, as with pressure, the higher the amplitude the faster the heating rate. With this said, excessive amplitude or force will have a detrimental effect on the weld quality, so optimisation is required - but once this process has been undertaken and the correct parameters found. The welding process can then be repeated with ease, giving an effective and strong bond. This is why ultrasonic welding is preferred for mass produced components.
Time, Distance, Power & Energy
The correct heat will be a factor based on the type of materials, type of joint and specification of the welding equipment. The traditional method of controlling the amount of heat is to weld by time, where the equipment operates for a fixed amount of time (a typical weld takes less than 1s). However, equipment now often includes the ability to weld and monitor in distance, power and energy in addition to time. With a properly trained operator, the correct selection based on the circumstances can give consistent results that allow for changes between materials being welded so that a great weld is reliably achieved.
At Xfurth, we specialise in ultrasonic welding – click here to check out our Guide To Ultrasonic Welding Machines and Tooling. You can also call us on 01582 436 000 to find out more.